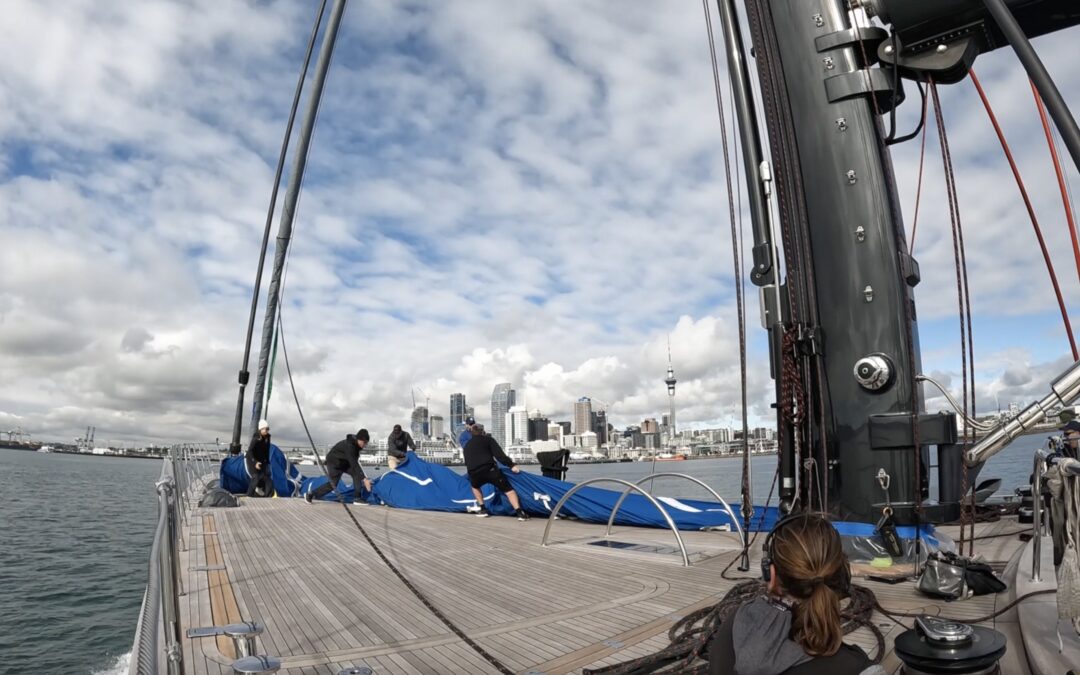
New Zealand – Auckland Sea Trials
S/Y Seahawk wraps up 10 months in Orams Shipyard in Auckland New Zealand. The sails and rigging are re-installed and we set off for sea trials over the course of 3 days to test everything.
S/Y Seahawk wraps up 10 months in Orams Shipyard in Auckland New Zealand. The sails and rigging are re-installed and we set off for sea trials over the course of 3 days to test everything.
After 11 months in Auckland, Seahawk has finally returned to the water and is on her way to New Caledonia, where she will cruise for the next two months. How lovely it is to finally see those sails up and feel the breeze as we cut through the water’s surface in the Pacific Ocean.
For a good few months of the refit in Orams shipyard, we were in the thick of finding new issues we didn’t plan for. These eventualities often mark a depressing period in any refit for the captain, crew and owners, as the continual stream of obstructive discoveries impacts the workload, cost, and duration of the project. However, we pushed through and found light at the end of the tunnel.
The major tasks were progressing, as the welding to the hull and stern tubes came to an end. Significant progress was being made elsewhere, with the rig components returning from service, and the masts completing the painting process.
On completion of the hull welding, the main hull and superstructure painting could continue, with the make-or-break paint shots on the hull; a huge area to paint, and it required to be as perfect as possible to avoid further delays to our schedule. I’m pleased to say that the Orams paint team achieved this, despite the winter weather in Auckland, resulting in a big sigh of relief from all concerned.
Completing this activity was key to the project flow, as we could start to accelerate toward the major milestones of removing the tent and re-assembling the boat. It IS amazing how quickly things do come together when all the pieces are ready to go. The masts were moved for ‘dressing’ (refitting the rig components), the tent cover came off, and 4 ‘crane days’ resulted in the majority of deck furniture and large fittings being re-attached.
Electrical power was also returned to the boat following the interruption necessitated by the welding work. This was a nerve-racking moment as many will know; re-energising systems after a long shutdown period, especially when so many electronic and computer-based systems are involved, can be highly problematic. We had an added complication, as so much wiring had been disconnected, and many 3-phase motors were removed and re-installed without being able to properly test. So there was a huge scope for issues here.
We got relatively lucky and only had a few issues that were solved with some remote support and the replacement of several system batteries through the boat, but no real show-stoppers. Phew! When we saw green lights on the sail system control PLC, I can assure some of us started to sleep a lot better.
This period is a manic and stressful effort for all concerned, with contractors all trying to squeeze into the same working spaces, crew scurrying around putting things together, and trying to remember where some parts are (it’s common to lose some bits and end up scratching your heads looking for them). Dave White and his rigging team were on a tight schedule too, as they had 2 and a half weeks to rebuild both masts, plus re-attaching all the antennas in readiness for the re-stepping date; a date fixed due to the availability of the crane and associated infrastructure needed. The interior crew gets to see the magnitude of the clean-up task too as protective coverings are removed. While these do prevent a lot of significant damage, there are always areas that need attention and need scheduling around the high activity going on.
However, with all the above taken into account, 3 weeks after completion of the final paint shot, Seahawk was ready to be picked up and put back in the water, and the masts were ready to go back in.
Following those crazy weeks, we finally reached the magic launch day. The original plan had us putting Seahawk back in the water on Monday, June 26th, but the weather was looking like it would have other ideas. With the necessity of a calm day for stepping the rigs immediately following launch, the yard made the call to bring things forward a day; Sunday 25th became D Day, and we were ready!
While lifting a 60m sailing yacht is never a trivial task, lifting one with a brand new paint job requires extra care. The launch becomes more time-consuming than the haul out, owing to the protection needed to prevent damage to the still-curing paint surfaces. The weather gods smiled at us and gave us a dry day ( a rarity in Auckland, regardless of the season). Foam pads and brown paper were applied to the hull in the way of the lifting strops and the machine driven around the boat. Sunday catering consisted of a wonderful fry-up brunch.
At around 14:00, everything was ready and the satisfying moment of knocking out the wooden blocks under the boat could begin. Then it’s time to stand back and watch as the Travelift carries out its manoeuvre to bring the boat over the launch pit. Then it’s the engineers, mechanics and plumbers’ big moment as the boat is lowered in to test the new valves and seals for the first time. Fortunately, aside from one reasonably sizeable leak on testing the fire main (due to a removed pipe section, unbeknown to those on board prior), the boat was watertight and the launch was considered a success (and one day ahead of schedule!)
If you’d like to know more, watch the video below, made by videographer Righardt Van Hyussten on Seahawk’s splash day.
written by Rotational Captain Steve
As the saying goes, despite “the best plan of mice and men”, yachts frequently have a tendency to unearth the unknown.
With Seahawk hauled out and safely choked on the hard, the next step was the disassembly of the boat for the painters, as well as the opening of sealed spaces and closed machinery for inspection by the ABS surveyor.
The process of a refit is often a voyage of discovery, and it can generate a range of new issues previously hidden from view. While experience is valuable in pre-empting these additional tasks, there’s sometimes the risk of finding new surprises.
Seahawk followed this mantra and gave us a few curved balls. The most significant one was the need to replace both stern tubes of the boat. These are pipes that run between the aft wall of the engine room to the hull, with the propellor shaft spinning inside it. These tubes are constantly full of seawater, which is highly destructive. This area of the boat is prone to gradual corrosion failure. In Seahawk’s case, there had been a rapid corrosion process taking place since some stainless steel sleeves had been fitted into the tubes at some stage for an unknown reason.
This presented a major new project for the yard with several hurdles, starting with the acquisition of the specific grade of aluminium required, and its paper trail of material approval for ABS. As it turns out, 5083-grade aluminium in 300mm thickness is a rare beast. We scoured the world to find enough for the job. Eventually, a dealer in Holland had some that could be acceptable.
The other major hurdle to this job was accessing the area for work; the boat’s main electrical distribution panel is directly above the starboard side stern tube, meaning that the vessel would have to go dead ship for the duration of the work, and the hundreds of cables meticulously disconnected and then reconnected following the extensive welding work that would be required; this electrical job represented more labor time than the metalwork itself.
Unfortunately, a job like this comes with penalties beyond just the unexpected costs associated with the extra work; Carrying out welding work on the hull must be in accordance with fire safety requirements, and it’s, of course, messy. Performing paintwork on the boat requires the use of solvents that are explosive, as well as clean room conditions, creating a major conflict between these two tasks, making scheduling a real headache for the management team, and inevitably delaying the completion of the overall project.
The other ugly feature of working on boats, especially aluminium ones, is corrosion in general. Steel boats “rust”; composite boats get “osmosis”; and aluminium boats suffer electrolytic corrosion, which is caused when two different metals have a continuous current in between them, as they are in contact with an electrolyte substance. Aluminium vessels are often referred to as “Alker Selzer boats”, as they essentially ‘fizz’ like the pills do when in seawater.
When performing a re-paint, dealing with corroded areas is always an add-on to the project, as it’s simply not possible to gauge the amount of corrosion until the painters start digging into the job. Yacht paint is not just a thin coat of color over the surface; The full job requires special primers applied to the bare surface, followed by several layers of a fairing compound that are used to create a smooth shape before a final primer. In Seahawk’s case, there’s also a metallic paint finish; a base color coat followed by layers of clear coat. In the event of corrosion of the metal substrate, all these layers have to be rebuilt and perfectly blended with the existing sound materials. This is time-consuming and tends to be an expanding job. Seahawk’s paint is 9 years old and was hiding a lot of corrosion under some particularly thick areas of the fairing, adding a great deal of time to the overall paint project and expected completion date of the boat.
These major developments, along with other smaller but nonetheless significant discoveries, pushed the duration of our refit from an estimated 6-month project out to a solid 9 months.
At this stage, the vessel is a “War Zone”, a daunting sight with so much taking place simultaneously and so much “destruction” to access the projects themselves.
As of now, Seahawk is being taken care of in Orams Marine and will be back in the water in June 2023. An exciting itinerary follows as we will continue to explore the South Pacific.
The following video, made by Righardt (dive instructor & videographer on board), captures some of our day-to-day experience in the shipyard. Enjoy!
Seahawk’s first journey of the Pacific Ocean came to an end in September 2022, after 9 months of cruising the waters of French Polynesia and Fiji.
Arriving in the city of Auckland was new for most of us on board. The cold, rainy weather of the New Zealand winter and the big city lights painted a scenario very different from the one we had gotten used to, in the tranquility and warmth of our previous destinations.
Seahawk’s prime purpose for her visit to Auckland is the run-up to her 10-year anniversary and ABS class certificate renewal. ABS (American Bureau of Shipping) is one of a number of globally recognized Class Societies, and it ensures that the vessel condition meets a long list of standards, that repairs are carried out correctly, and it ultimately certifies to the flag state that the vessel is materially seaworthy and unlikely to cause pollution or other dangers in operation. The boat’s class certificate lasts 5 years (subject to annual inspections). At renewal, the vessel undergoes a detailed and fairly invasive survey inside and out to check the condition of parts that are not normally accessible.
Amongst many other things, the survey includes: measuring the thickness of the hull, an overhaul of the main machinery (to a level depending on the total running hours usually), an inspection of all hull valves that keep the water out, and a thorough inspection of the shaft line.
As a 10-year survey involves extended time out of the water, it is usual to carry out an overall refit of the vessel at the same time. In Seahawk’s case, this meant a full repaint, and the opportunity to remove and overhaul the mast and rigging, which must also be carried out on a similar periodic basis. This project was a major event and would be expected to take a minimum of 6 months to complete, considering no eventualities or last-minute surprises.
The planning began a year in advance. After considering several options, Auckland seemed like the best overall fit for our intended movements and the availability of suitable facilities. Orams Marine was our selected shipyard, and a plan was drawn up to bring the project together.
So come September and there we were, in the City of Sails, ready to get to work. But first things first, masts and rigging had to be removed, and the boat had to come out of the water.
Pulling a Panamax rig from a yacht is no mean feat. The task requires the largest mobile cranes available, and a well-thought-out plan to lift the mast and lay it down on the ground; The combined area the masts need while assembled is around the size of a football pitch. The responsibility for this part of the project was taken by Dave White, of World Spar Services, and assisted by the team at RigPro in Auckland.
The rig pull ended up going by the numbers and was completed in one day. Then, the massive disassembly of the two spars followed to reduce their footprint as quickly as possible.
Shortly after, Seahawk got removed from the water. In the last 3 years, she has been hauled 3 times, each time by a different method. In Italy, she was dry-docked; in Mexico, a Synchro lift was used, and now it was the turn of an 820T travel lift to do the job. Again, the job went smoothly and the boat ended up securely blocked in the corner of Orams’ hardstand area ready for scaffolding and tenting.
And now, the real work begins.
If you would like to know more, dive instructor and videographer Righardt made the following videos to document the process. Enjoy!